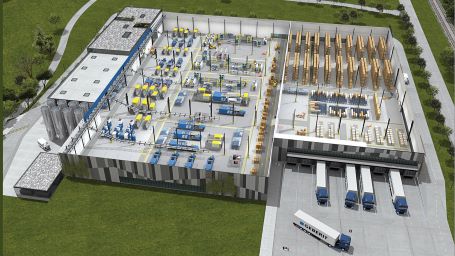
The Significance
Creating a manufacturing function that embodies the capacity, intelligence, and expandability in support of corporate growth and cost goals is foundational to corporate value.
The Effect
A good manufacturing model and management approach is one where manufacturing is a service function to the rest of the company. It is the responsibility of manufacturing to always say yes to corporate growth needs. There will be costs and timelines associated with these requests but if modeled and built properly, your manufacturing team will be in a position to analyze, quantify and provide a how to plan.
Key areas to be considered, discussed and serviced:
Demand and Throughput Planning – Focused plans capturing; annual, quarterly, monthly, weekly and daily capacity demands
Manufacturing Model Design – Identification of in-house vs. external manufacturing processes, supporting supply chains, and process flows
Plant layout – Block level to detailed layouts with flow lanes, work cell layouts, facility expansion needs and construction planning
Material Management – Shipping/Receiving, material flows & handling, inventory storage (raw, WIP and finished, goods), ERP connections
Sales Channel Considerations – How to prepare for and service sales orders from multiple channels: Direct, Resellers, Stocking Distributors, Service Support Spares
Order fulfillment Considerations – Direct, 3PL, eCommerce and SLA contract fulfillment considerations
Business and Technical Decision Support Systems – S&OP, S&IP, ERP, MRP, MPS, MES, PLM, QMS solutions, designs and implementation planning
- Implementing Demand Planning process that create actionable Purchasing plans and Master Production Schedules
- Selecting and designing integrated ERP solutions that support Finance, Production, Purchasing, Supply Chain and Field Service
- Product Lifecycle Management selection via implementation, including part numbering schema’s, BOM structuring, ECO controls and effectivity management across the supply chain
- Quality data management from the factory floor to management dashboards
Manufacturing KPI Creation – KPI’s that proactively measure; factory effectiveness, process costs, process yields, inventory management, manpower utilization, and new product introduction effectiveness
Technical Operations and Team Constructs – Manufacturing Engineering, Test Engineering, Process Engineering and Quality Engineering. Distribution of test and quality management tools, test stations, data capture and reporting means amongst all external and in-house groups responsible for product quality and integrity.
Regulatory and Audit Compliance Planning – ISO, UL, FDA, CSA, TUV considerations and factory record creation/retention process
State and Federal VOC, Haz Mat, Flammable Compliance – Considerations and impact on factory control procedures, physical storage requirements, process constraint considerations