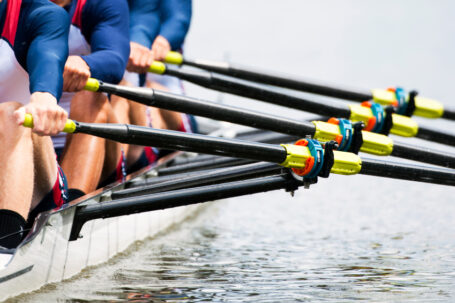
The Significance
Organizing your Manufacturing, Supply Chain, Technical Operations and New Product Introduction teams into an integrated whole, creates the foundation for corporate success.
The Effect
How teams are structured within their areas of responsibility as well as how relationships are set with all corporate functions; Finance, Development, Sales, Marketing, Customer Service and Executive Management is paramount to successfully executing corporate strategy goals.
To execute on these goals, consideration must be given to the identification and selection of internal and external resources, the organization and leadership of these resources, and the needed on-going management controls.
How you create and structure your teams to align strengths and offset weakness, while providing the management structure to lead these teams, is a foundation of my offering.
Key areas to be considered, discussed and serviced:
Team resource planning – Reflecting the Manufacturing model, teams need to be aligned with the mission at hand and capable of supporting the company growth now and into the future.
Manufacturing/Process Engineering – What specific skills, experiences and numbers are needed to support production processes across the supply chain. Workmanship standards, SOP’s that incorporate production methods, tools, EHS and MES data collection.
Test Engineering – Skills to design and implement functional test equipment and full ATE’s that collect, analyze and publish test data (down to the serial number) in real time, across the supply chain is key to linking all production processes into a single actionable data flow.
Quality Engineering – Experience designing and implementing statistical process controls across the supply chain that provide accurate and timely process and product yields. Supported by the ability to delve into failures and lead yield improvement projects is one of the more important contributors to improving product COGS.
Production Management – Ability to quantify the needed factory capacity, factory floor resources, production schedules, efficient material flows and inventory controls & management is core to daily factory efficiency and worker productivity.
Supply Chain Management – Key to this functional area are the skills and experience to source, qualify and manage external suppliers; negotiate supply & services agreements; align material flows with demand plans; ensure raw, WIP and finished goods inventory levels are matched with shipment demands & inventory investment targets while ensuring ERP inputs & outputs are accurate, timely and auditable.
Purchasing – Skilled buyers and planners are the guardians of inventory expenditures, efficient in-bound flow of materials supporting JIT assembly, early warning sentinels of impending stock-out events (and solution’s providers), and central figures in ensuring ERP inputs & outputs are timely & accurate.
Logistics – May be separate or folded into another function but the function is central to ensuring shippable products arrive on time, without damage at an efficient cost. All worldwide demand is picked, packed and shipped with the correct shipping documentation (domestic and international), clears Customs (as needed) and ERP inputs & outputs are timely and accurate.
NPI Program Management – An essential function that bridges the transfer of designs from Development into Manufacturing. Using a prescribed phase gate approach that is matched to the needs of the company, this team/individual provides the leadership that ensures the transfer process from ideation to mass production encompasses the voice of the customer, corporate go to market requirements and meets corporate financial goals. Depending on the number, frequency and diversity of products to be launched, this function may consist of:
- NPI PM – Individual program managers who manage a small number of NPI projects
- PMO – A full program management office staffed with multiple PM’s and has expanded corporate responsibilities and visibility
Facilities Management – A strong facilities management organization forms the backbone for all other functions of the company to quietly go about their responsibilities. Depending on the needs and complexity of the company, this function handles:
- Daily office needs, for example; access security, cleanliness, office environmental comfort and utility expenditures
- Site HVAC, electrical, plumbing, construction needs. Internally managed with on-staff trades people and/or selection and oversight of service partners.
- Construction project oversight. Project leadership and compliance with local, state and federal regulations
EHS – Employee health and safety inclusive of site visitors, is essential to uninterrupted operation of the business. Recognition and need of this function is a need to be addressed. Where in the overall organization this function sits is a discussion to be had.
Alignment and organizational controls with all corporate functions – Manufacturing and all of its organizational components is just one function within the organization. Identifying the management controls needed to ensure smooth communications and accountability across all teams is essential. Typical organizations to be included in the assessment are:
- Development Engineering/R&D
- Finance
- Sales
- Marketing
- Customer Success
Taken as a whole, the organizational structure and management controls should promote self-determination amongst team members, provide an environment where individuals are expected to take on challenges and if managed properly, see team success as their means to self success.
I can help with the construct and management controls that promote these objectives.